The History of Parcel Couriers: From Ancient Relays to Modern Delivery Giants
Written at May 30, 2024 11:35:41 AM by Justin O'Donnell
When we think of parcel couriers, we probably don’t think of Ancient Mesopotamia or Bronze-Age Egypt. However, the journey of parcel couriers is a fascinating tale that spans thousands of years, showcasing humanity's innovative knack for overcoming the challenges of distance and time. This blog post delves into the history of couriers, tracing their evolution from the cradle of ancient civilization to the sophisticated systems we rely on today.
Ancient Beginnings: The Birth of Communication Networks
We can trace the concept of a courier system back to ancient civilizations, where the need to send messages and goods across vast distances gave rise to the first organized delivery services.
Ancient Egypt and Mesopotamia:
Around 2400 BCE, the Egyptians used couriers to transport documents carved on clay tablets. Similarly, the Mesopotamians developed early postal systems to facilitate communication across their empires. Interestingly enough, no private post systems existed in the ancient world, but many made use of state communication apparatuses to send clay tablets and papyri over great distances.
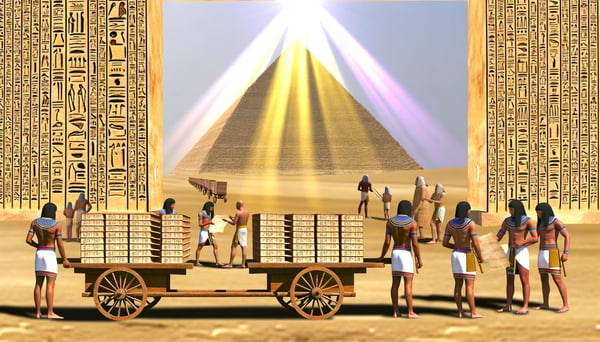
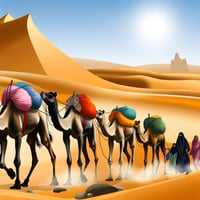
Persian Empire:
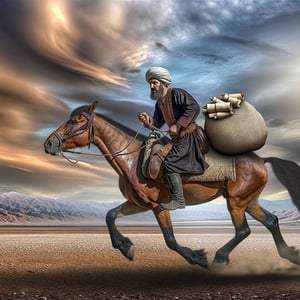
The Persians, under King Cyrus the Great in the 6th century BCE, established one of the earliest and most efficient courier systems known as the "Angarium." This network used relay stations and horsemen to ensure messages could be swiftly delivered across the empire. The famed Greek Historian, Herodotus, even praised this system in his Histories (Bk. 8.98) for its resilience and relentless couriers who could travel in relays at high speeds, no matter the weather.
If one were to visit the central post office in New York, you would see one of his quotes on a sign that reads: “Neither snow nor rain nor heat nor gloom of night stays these couriers from the swift completion of their appointment rounds.”
Roman Empire:
The Romans advanced courier systems further with the creation of the Cursus Publicus, a state-run postal service that utilized a network of roads, waystations, and fresh horses. This system enabled the rapid dissemination of information across their vast territories.
The Romans employed couriers (iuvenes) who traveled all the way from sender to receiver or ran relays. The messengers enjoyed state-sponsored rations and fresh transport (vehicula) at regular stations along the 75,000 miles of Roman road network, which allowed messages to travel a staggering 50 miles a day.
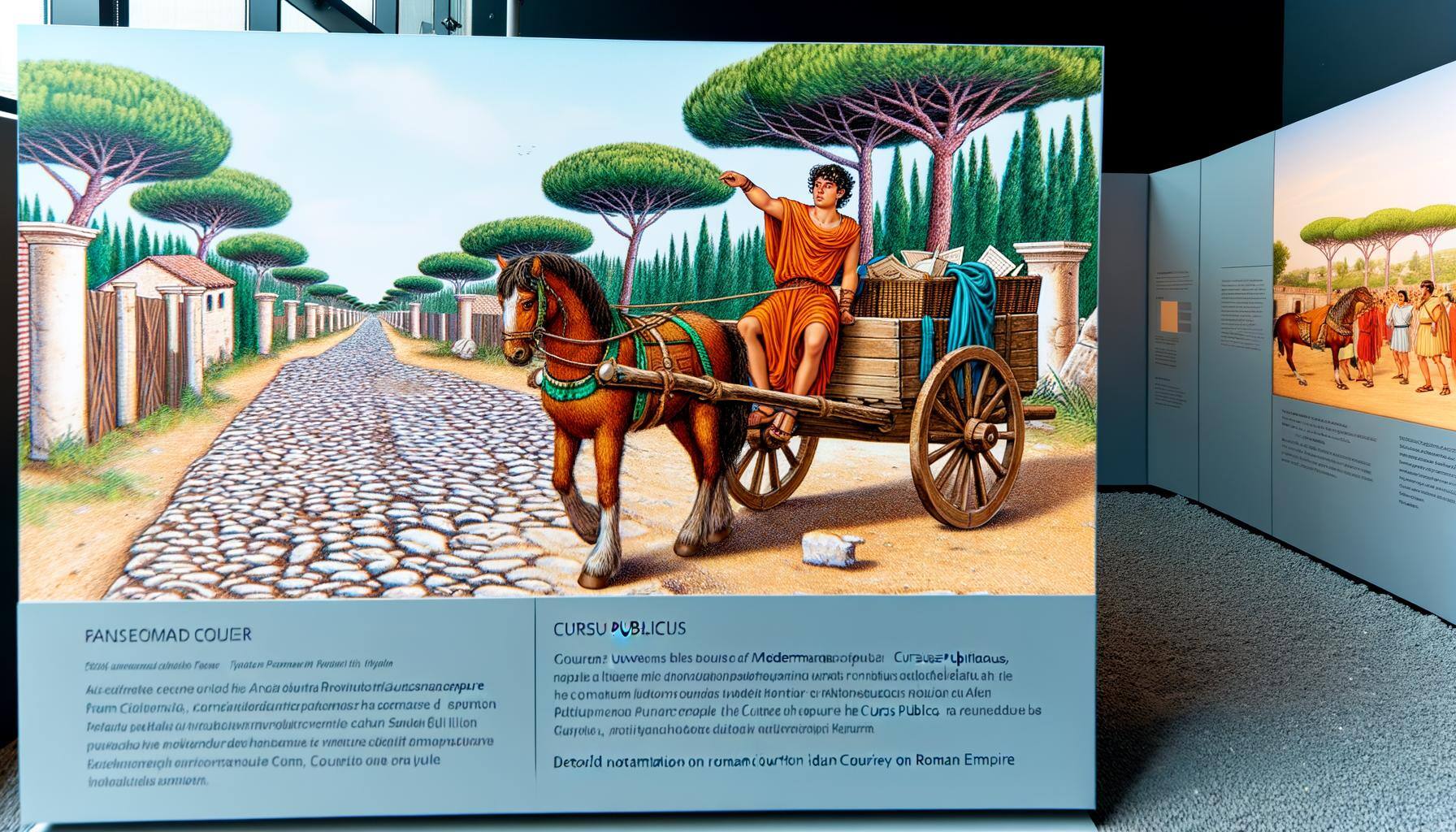
A courier, known as an iuvene, working for the Roman Empire's Cursus Publicus, carries letters and parcels for delivery across the Roman road system.
Medieval and Early Modern Innovations in Parcel Delivery
As civilizations grew and trade expanded into the Middle Ages, the need for more efficient courier services became paramount.
Silk Road:
During the medieval period, the Silk Road served as a major conduit for trade and communication between the East and West. Caravanserais, or roadside inns, were established along the route, providing rest and resupply points for couriers and merchants. Constantinople became a “hub,” but the cost of maintaining the old Roman Cursus Publicus became too onerous for the Eastern Roman Empire (Byzantine Empire). In the sixth century, the historian Procopius alleges that Emperor Justinian dismantled most of its sections, with the exception of the route leading to the Persian border.
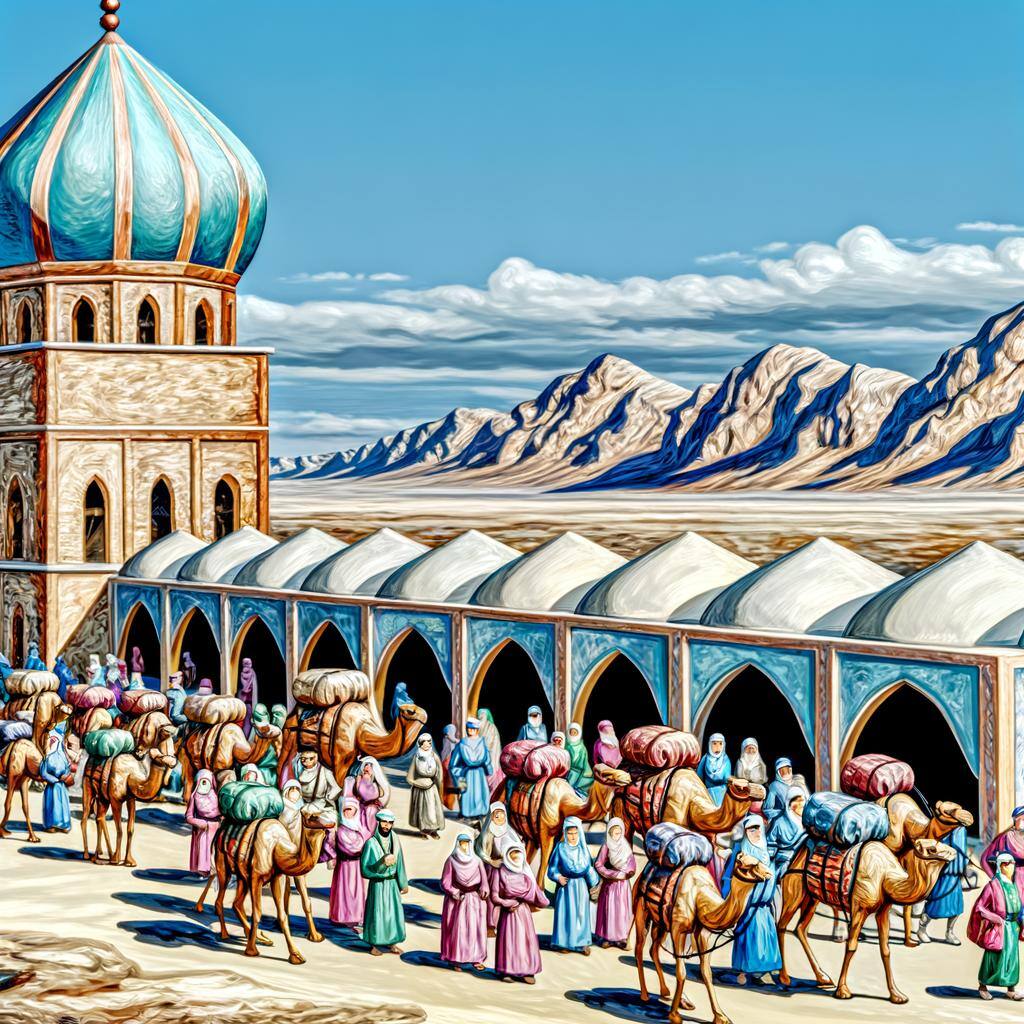
European Postal Services:
In medieval Europe, monarchs and noble houses established their own courier systems. Notably, in the 13th century, the Holy Roman Empire developed a reliable postal network under the direction of the House of Thurn and Taxis, which became the de facto postal system for much of Europe by the 16th century.
Colonial America:
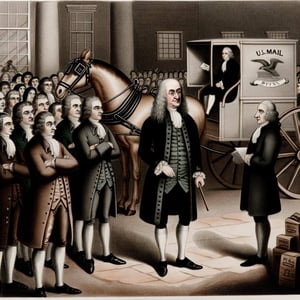
In the American colonies, Benjamin Franklin played a crucial role in organizing the postal service, becoming the first Postmaster General in 1775. His efforts laid the groundwork for what would become the United States Postal Service (USPS).
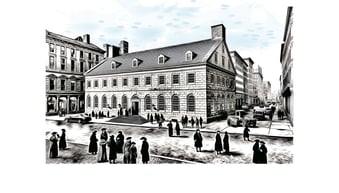
The Industrial Revolution: A Turning Point for Parcel Couriers
The Industrial Revolution of the 18th and 19th centuries brought about significant advancements in transportation and communication and revolutionized parcel delivery.
Railways and Steamships:
The advent of railways and steamships drastically reduced delivery times and expanded the reach of courier services. Goods and messages could now be transported faster and more reliably than ever before.
Uniform Penny Post:
Introduced in the United Kingdom in 1840, the Uniform Penny Post standardized postage rates and made mail delivery affordable for the general public. This system set the stage for modern postal services.
Telegraph and Telephone:
The invention of the telegraph and later the telephone introduced new methods of communication, complementing traditional courier services and facilitating faster decision-making processes in business and government.
The 20th Century: The Rise of Modern Courier Companies
The 20th century witnessed the emergence of the courier industry as we know it today, characterized by rapid advancements in technology and logistics.
Founding of Major Couriers:
Companies like United Parcel Service (UPS), founded in 1907, and Federal Express (FedEx), established in 1971, transformed the industry with their focus on efficiency, reliability, and customer service. They introduced innovations such as overnight delivery and real-time tracking.
Airmail:
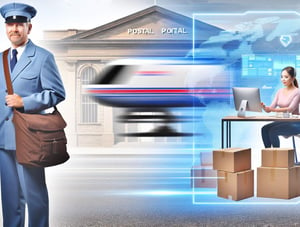
The introduction of airmail services significantly reduced international delivery times, making global commerce more accessible. The establishment of dedicated air cargo services further boosted the efficiency of parcel delivery. On May 15, 1918, Lt. James Edgerton piloted a Curtiss Jenny from Philadelphia to Washington, DC, marking the inaugural scheduled airmail flight. Despite its challenging beginning, this milestone ultimately altered both the postal service and the airline industry forever.
Automation and IT:
The late 20th century saw the integration of automation and information technology in courier services. Automated sorting systems, computerized tracking, and online booking platforms streamlined operations and improved customer experience.
The 21st Century: The Age of E-commerce and Same-Day Delivery
The turn of the century brought about the digital revolution, transforming the parcel courier industry to meet the demands of e-commerce and globalization.
E-commerce Boom:
The rapid growth of online shopping created an unprecedented demand for efficient parcel delivery services. Companies like Amazon introduced their own logistics networks, pushing traditional couriers to innovate and expand their capabilities. By 2020, Wal-Mart and Target achieved store networks that could reach 99% and 94% of the U.S. within 60 minutes, respectively.
Same-Day and Drone Delivery:
To meet consumer expectations for speed, couriers have developed same-day delivery services and experimented with cutting-edge technologies like drones and autonomous vehicles. These innovations promise to further reduce delivery times and increase efficiency. Companies like Wing are experimenting with medical, grocery, and meal drone deliveries in urban areas.
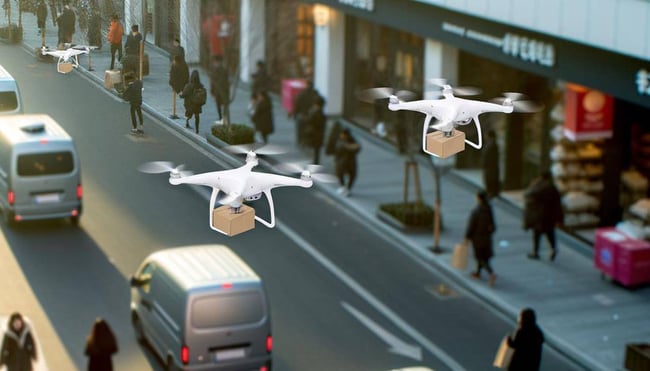
Sustainability Initiatives:
In response to environmental concerns, courier companies are investing in sustainable practices. Electric delivery vehicles, carbon-neutral shipping options, and eco-friendly packaging are becoming standard offerings. As an example, the USPS plans to deploy over 66,000 electric vehicles by 2028.
Conclusion
From ancient empires to modern-day logistics giants, the history of parcel couriers is a testament to human innovation and adaptability. As technology continues to advance and consumer expectations evolve, the courier industry will undoubtedly keep innovating to meet the challenges of tomorrow. The journey of a parcel, once a feat of endurance and resourcefulness, is now a seamless process powered by technology and driven by a relentless pursuit of efficiency and innovation.
Justin O'Donnell
BlueCrest
0 comments